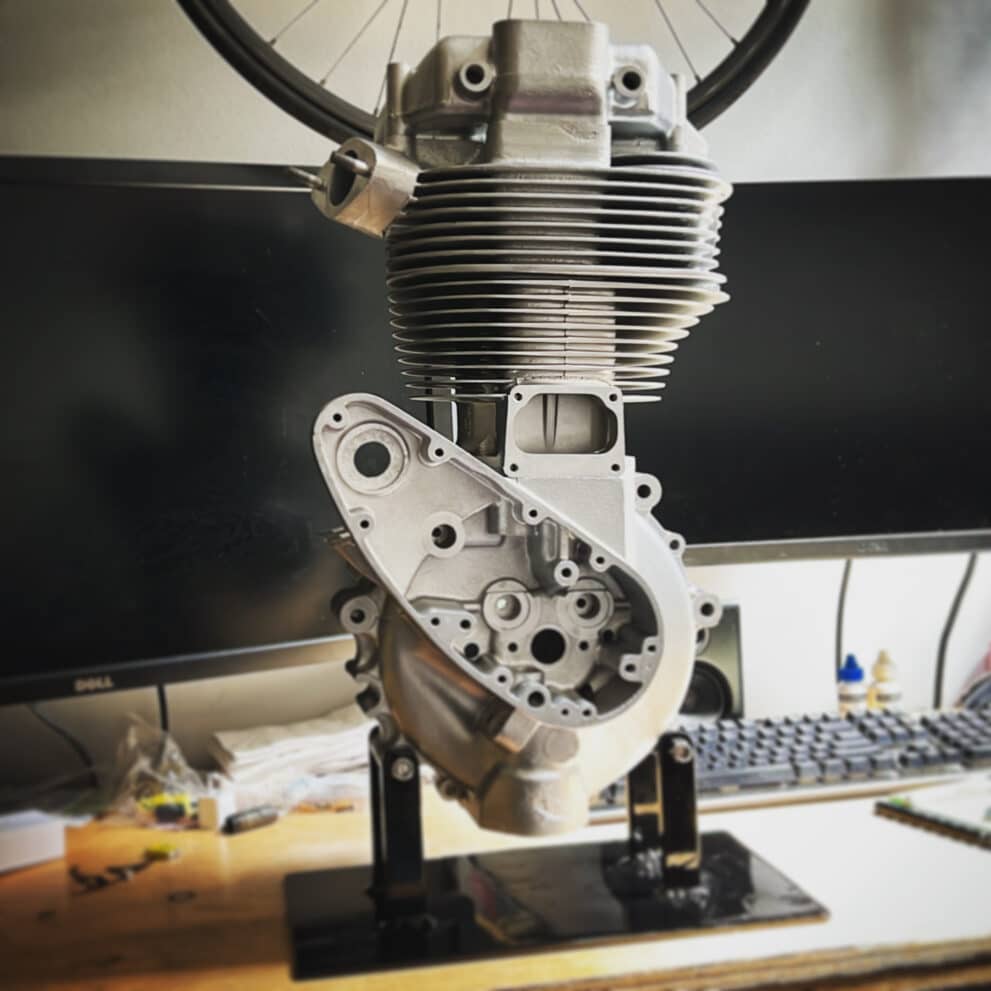
November 4, 2023
I have been working on a BSA DBD34 Goldstar 500cc single cylinder motorcycle for several years now. This has been a back burner project as every time I make a little progress, another motorcycle needs some TLC. The Goldstar gets put aside and then my time frees up and we find time to make a little progress. Last year Larry and I took some time off the Rickman project and machined a pair of valve guides out of manganese bronze for the Goldstar. The idea is to use stainless steel 7mm valves, and the challenge is that no one makes 7mm valves for the BSA 500. However, 7mm valves are common on American cars, and the BSA 500 has just enough space to fit Dodge and Chevy valves, which is a huge cost savings over specialty valves made for the Gold star. The 1.890” intake valve is from a 350 Chevrolet and the 1-5/8 exhaust valve is from a 5.7 liter Dodge.
These valves will also require special valve guides, which are not readily available through any parts supply that we know of. With the addition of Kibblewhite valve seals the guides had to be machined to accommodate them. We machined tapered plugs out of Delrin for the valve pockets to center the reamer we used after pressing out the old guides, in preparation for the new guides.
We then pressed the new guides into the head by heating the head in the oven to 300 degrees to expand it, and freezing the guides to be pressed into the head to contract them. Then we used a special valve guide hone to obtain the correct clearance between the valve stem and the guide, and when the fit was correct, we started the valve and seat grinding.
Both of the newly sourced valves had stems far too long for the Goldstar. A call to Manley valves revealed that the valves can be cut to length and have groves machined into them for the keepers.
I found a Sioux valve grinding machine on Craigslist at a very inexpensive price, which I bought. I also bought a bunch of new grinding stones and we went to work. We ground the new valves to 46 degrees and then ground the seats to 30, 60, and 45 degrees respectively.
After lapping in the valves, we compressed the new beehive springs and retainers to the correct stack height and measured and marked for the keeper grove. I ground a carbide tool bit with the required radius for the keepers, machined the valves and installed them in the head, once again checking the stack height using shims if necessary.
Everything went well and all we had to do now was cut off the excess valve stem length, grind it smooth and heat treat the valve tip by heating the last ¼” of the valve red hot with an oxyacetylene torch and quenching the valve tip in water.
Once the valves were fitted I had them hard finished in Chromium Nitrate by a company in North Carolina, Calico Coatings. This in theory should help minimize valve wear and hopefully avoid re doing this job for a long time. This Goldstar head is finally ready to go!
Comments