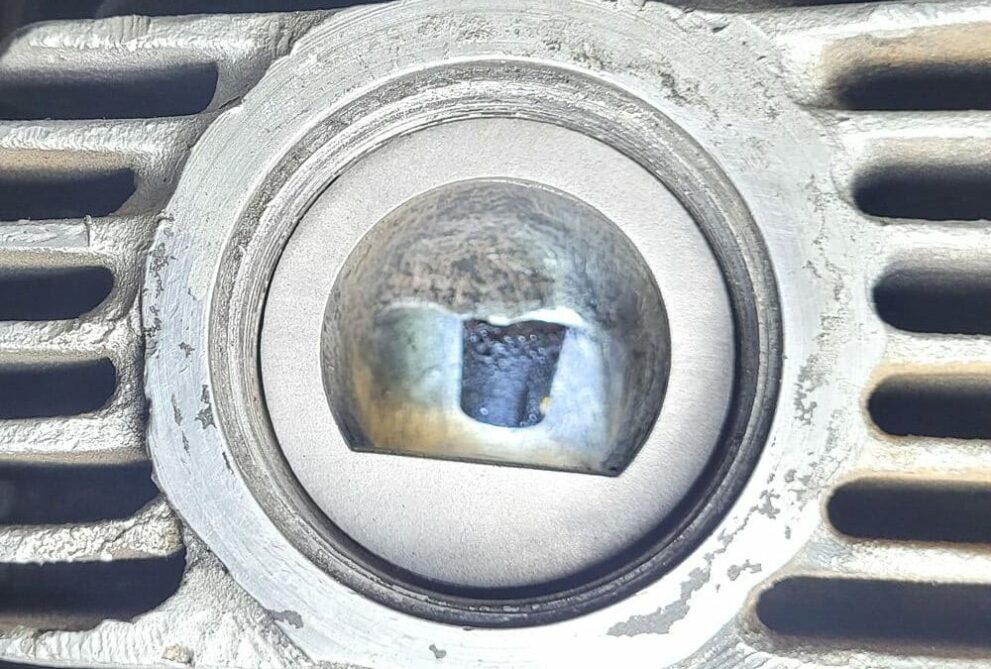
Several years ago I remember coming across an interesting exhaust manifold gasket for a Ford V8. This gasket had a clever design where it folded down into the exhaust port, effectively raising the exiting exhaust gases. This setup was meant to minimize reversion—those pesky exhaust pulses that try to sneak back into the combustion chamber.
Fast forward to earlier this year, I was fortunate enough to receive some documentation and drawings from Jim Schmidt, a well-respected figure in the Norton community known for his racing expertise in performance tuning and engine modifications. Jim had sourced detailed materials for the Harley-Davidson XR750 ports and the C.R. Axtell-developed ports for the Norton, which also included comprehensive diagrams of the exhaust ports.
Initially, I thought the project would be relatively simple—just weld a tab to a washer and fit it into the Norton head, and that would be it. However, as I dug deeper into the design, it became evident that crafting an adapter for the Norton cylinder heads would not be as straightforward as I had hoped. The design challenges were far more intricate than anticipated, demanding a great deal of ingenuity and precision to get everything just right.
For those unfamiliar, the XR750 is a motorcycle developed by Harley-Davidson in the late 1960s. Originally designed for flat track racing, the XR750 quickly made a name for itself as one of the most successful racing motorcycles ever built. The caveat being AMA rules favoring Harley Davidson and dwindling flat track racing public interest allowing the XR750 to remain top of the heap from 1972 to 2008.
What makes the XR750 particularly interesting, is its highly developed cylinder head, and it is probably the most developed air cool engine in history. I have covered some of the intake port information in a previous articles about building a intake port sleeve. The exhaust port design of the XR750 is highly efficient, making it a valuable reference point when modifying or designing components for other classic motorcycles, like the Norton. By examining drawings of teh XR750’s port floors, I was able to shape my own designs, especially when working to improve the exhaust flow and reduce reversion in Norton engines.
But getting the exact arc was just half the battle. The real challenge was tapering the sides of the floor into the port smoothly. I went through a ton of 3D-printed models in stainless steel, tweaking and adjusting to nail the shape. After weeks of experimenting, I had a lightbulb moment.
Jim did me a huge favor without even knowing it. In his drawings, he meticulously documented the differences between the Norton exhaust ports and the XR750 port floors. This was gold for me because it gave me a precise shape for the port floor that I could use as a reference for designing the slope of the port.
The real challenge was tapering the sides of the floor into the port smoothly, tightly, securely, and in a way where it would fit consistently. I went through a several 3D models as well as 3D-printed models in stainless steel, tweaking and adjusting to nail the shape. After weeks of experimenting, waiting for prints and failing I finally had a lightbulb moment.
Most new smartphones have the ability to be a 3D scanner as they have a Lidar scanner built into them. I took several 3D scans of a spare Norton Cylinder head I have. These scans provided an accurate view of the port and allowed me to build and design the exhaust port fitting inside the 3D model of the port. This allowed me to build the right width and shape and get past the details I was stuck on.
I sent off the first of these new models made from 3D scans to the 3D printer and a week later it became clear that this is the right path forward. A single revision to remove some material and make these a little easier to manipulate to get a more exacting fit even with the variations of Norton heads. I was then able to fit and test these in my Norton. I do not have a dyno so I cannot quantify what the gain is, but there is an improvement, and the top end seems to have picked up. I have successfully fit these in a 750 and 850 MK3 Norton and they seem to work as expected. The 3D printed stainless steel has held up well in the exhaust port even while I have been adjusting the tune due to the intake sleeves requiring some refined intake port tuning, which has involved some long sustained high rpm pulls.
I have sent over the 750 fitting to Jim Schmidt to have him manage the Norton production of these. The initial batch sold out in two days, completely shocking to me. I hope to have more of the 750 as well as the 850 MK3 fittings over to him by mid September. Hopefully I have the intake tube manufacturing issues sorted out by mid september as well as he can post those up for sale as well. The 750 and early 850 exhaust fitting can be found on JS Motorsport. I will link the 850Mk3 as soon as it lands.
Comments